Turbine Governor Control (TGC)
As previously mentioned, the governor regulates the active power flow into the turbine by controlling the position of the control valve. A hydraulic governor can be modeled as an integral controller that takes feedback from the turbine’s actual rotational speed. Figure 1 illustrates the governor’s operation in speed - control mode.
The turbine’s actual speed is compared against the reference speed (corresponding to the nominal grid frequency). The resulting speed error signal (∆ωᵣ) is then fed to the governor. Based on this error signal, the governor adjusts the control valve position: if a positive error signal is detected (indicating the actual frequency exceeds the nominal frequency), the governor slightly closes the valve; conversely, it opens the valve when a negative error signal is received.
“R” represents the governor’s droop setting, typically ranging from 3% to 8%. Mathematically, it is defined as:
R = (per unit change in frequency) / (per unit change in power)
Droop settings are critical for the stable parallel operation of multiple generating units, as they determine how load is shared within a control area. Units with a smaller droop value will automatically assume a larger share of the load.
Control Area
In a power system, generating units and loads are distributed across vast geographical regions. To maintain stability, the entire grid is divided into smaller control areas (primarily based on geography). This division enables:
- Efficient load flow calculations
- Precise control of frequency and power balance
Within a control area, multiple generating units and loads coexist. Subdividing the power system into control areas serves several key objectives:
1. Load Frequency Control
This framework enables the application of load - frequency control methods to maintain grid frequency—a concept explored in greater detail later.
2. Determination of Scheduled Interchanges
If a control area’s generation falls short of its load demand, power flows into the area from neighboring control areas via tie lines (and vice versa).
3. Effective Load Sharing
Load demand varies throughout the day (e.g., lower at night, peaking in the morning and evening). Control areas simplify the process of:
- Allocating load across units based on projected demand and unit capacity
- Calculating scheduled power interchanges with other control areas
Power Balance
Electrical energy is consumed in real - time (it cannot be stored on a large scale). Thus, power balance is a fundamental requirement:
Power Generated (P₉) = Load Demand (Pd) + Transmission Losses (Pₗ)
Transmission losses typically account for ~2% of generated power and are often neglected when focusing on frequency control. For simplicity, we approximate:
Power Generated (P₉) ≈ Load Demand (Pd)
Frequency Variation
Grid frequency fluctuates due to mismatches between load demand and generation. While minor deviations are stabilized by system inertia, significant gaps (e.g., unit trips, large load changes) can cause frequency to vary by ±5%. Key scenarios include:
- Unplanned outages of generating units or transmission lines
- Sudden connection/disconnection of large loads
In most cases (e.g., unit/line trips, large load connection), demand exceeds generation, causing frequency to drop. Conversely, if a transmission line serving a large load trips, generation may exceed demand, causing frequency to rise. Though the system responds oppositely to these scenarios, understanding frequency dips suffices to grasp both behaviors.
Why Frequency Dips Occur
Two inherent system behaviors drive frequency dips:
1. Load Dampening
Induction motors (e.g., household fans, industrial drives) dominate grid loads. Their power consumption is frequency - dependent: a 1% frequency reduction typically reduces active power consumption by ~2% in large systems. When new loads connect, frequency drops, and existing induction loads automatically consume less power—partially mitigating the demand - generation gap.
2. Kinetic Energy Release from Turbine - Generator (TG) Sets
Conventional TG sets have massive rotors (often >25 tonnes) spinning at 3000 RPM (for 50Hz grids). When demand exceeds generation, these rotors temporarily supply stored kinetic energy (for 3–5 seconds, depending on inertia). As rotors slow down, grid frequency drops.
Frequency Control
Load - frequency control (LFC) restores grid frequency to its nominal value after demand - generation mismatches. Two tiers of control exist:
1. Primary Frequency Control
At the unit level, the turbine’s governing system adjusts speed (and thus frequency). As shown earlier, each unit modulates steam input based on frequency deviations. The full primary control loop for a generating station is depicted in the figure below.
2. Secondary Frequency Control
This involves coordinated control across multiple units in different control areas, ensuring long - term frequency stability and optimal load sharing.
Primary Frequency Control Limitations
Primary frequency control alone results in a steady - state frequency deviation, influenced by the governor droop characteristic and load frequency sensitivity. This occurs because individual units adjust speed without considering where new loads are connected or how much load is added. Without such contextual assessment, power balance cannot be fully restored, and frequency deviation persists. Following primary control actions, the steady - state frequency error may be either positive or negative.
Secondary Frequency Control
Restoring system frequency to its nominal value requires secondary control, which accounts for new load locations and adjusts reference setpoints for selected units. When load increases in a control area, generation within that area must rise to:
- Maintain demand - generation balance at the control area level
- Keep scheduled interchanges with adjacent areas within pre - defined limits
To achieve this:
- Automatic Generation Control (AGC) assigns specific units in each control area for secondary control.
- A frequency bias loop is added to their control systems, providing real - time corrective signals based on load flow calculations.
Once revised load setpoints are issued, units begin adjusting generation. Due to the mechanical nature of power production, it takes 25–30 minutes for units to reach their scheduled outputs. When all generating stations achieve target generation, power balance is reinstated, and frequency returns to nominal.
The overall response of the system with the primary and secondary frequency control can be understood by the graph below.
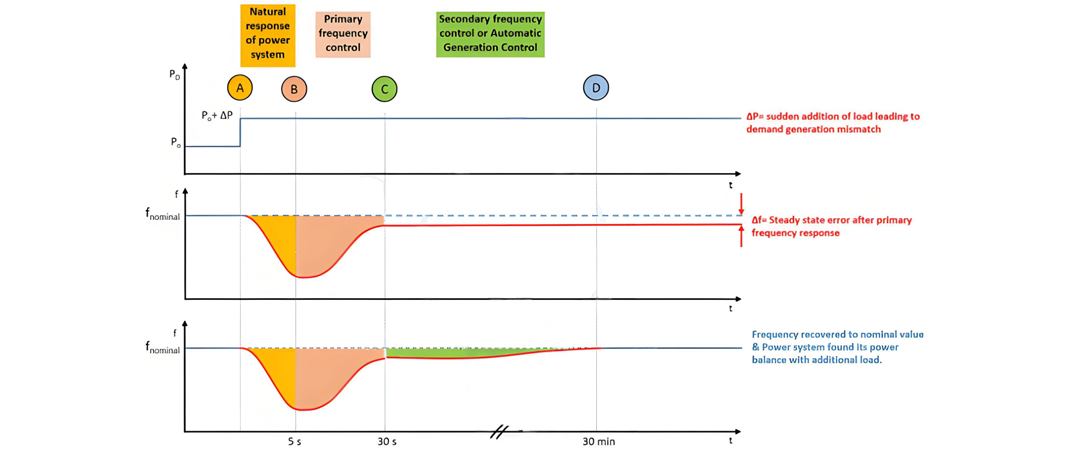
System Response to Load Increase (A-B-C-D)
A-B: Transient Kinetic Energy Release
Before point A, the system operates in power balance. At point A, load suddenly increases from P₀ to P₀ + ∆P. A 3–5 second delay occurs before the governor responds. During this interval, the rotor's stored kinetic energy supplies the excess load, causing rotor speed to drop and frequency to dip to a minimum value f₁.
B-C: Primary Frequency Control Action
At ~5 seconds, the governor initiates speed control, increasing steam input to restore rotor speed. This phase lasts 20–25 seconds (dependent on the frequency dip magnitude). As discussed, primary control alone leaves a steady - state frequency error ∆f due to governor droop.
C-D: Secondary Frequency Control (AGC Activation)
Once frequency stabilizes, secondary control (via AGC) adjusts generation for selected units in each control area. This process considers:
- New load reference setpoints
- Frequency bias signals from real - time load flow calculations
Generation adjustments are limited by the units’ design ramp rates, taking several minutes to complete. Upon finishing, scheduled interchanges return to pre - calculated values, and the system achieves a new power balance with nominal frequency.