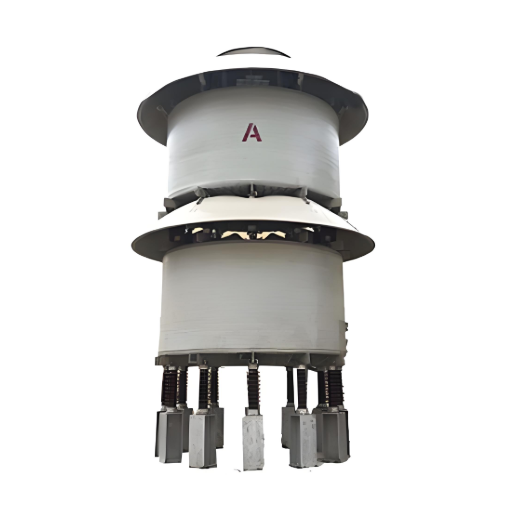
1. Challenge: Output-Side Voltage Spikes (du/dt > 5000 V/μs) from 550kW VFDs in Steel Rolling Mills
During steel rolling production, motors (especially main drive motors for rolling mills) are subjected to intense impact load variations, rapid starts/stops, and frequent bidirectional rotation switching. These operating conditions pose severe challenges for VFD (Variable Frequency Drive) systems, particularly in high-power (550kW) applications. A core issue is the generation of extremely high voltage slew rates (du/dt) on the VFD output side, manifested as:
- Extremely High du/dt: Spike values exceeding 5000 V/μs. This typically arises from:
- The very high switching speed of IGBT devices inside the VFD.
- The parasitic capacitance and inductance effects of long motor cables (especially interacting with the rise/fall times of the VFD's PWM waveform).
- Impedance mismatch issues between motor insulation characteristics and the VFD output pulses.
- Severe Consequences:
- Motor Winding Insulation Damage: Extreme du/dt can puncture motor winding insulation, leading to partial discharge, accelerated insulation aging, and ultimately causing motor failure or breakdown.
- Bearing Currents and Electrical Erosion: High du/dt, through stray capacitances, generates common-mode voltage, leading to bearing currents. This causes bearing electrical erosion, increased noise, elevated temperatures, and reduced bearing lifespan.
- IGBT Module Overvoltage Stress: Reflected and superimposed spike voltages can cause the IGBT to experience instantaneous voltages exceeding its rating, increasing the risk of module failure ("blowing up").
- Electromagnetic Interference (EMI): High-frequency voltage spikes generate strong conducted and radiated interference, affecting nearby electronic equipment.
- Reduced System Reliability: The overall system failure rate increases significantly, leading to unplanned downtime and impacting rolling efficiency and continuity.
2. Solution: FKE Type Three-Phase Output Reactor (Nanocrystalline Core)
To address the aforementioned high-voltage spike problem, we recommend installing an FKE Type Three-Phase Output Reactor on the output side of the 550kW VFD. This solution is specifically designed to suppress high du/dt and high-frequency interference.
- Core Equipment: FKE Series Three-Phase Output Reactor
- Key Features:
- Core Material: High-performance Nanocrystalline alloy
- Possesses extremely high magnetic permeability and ultra-low core loss (especially in the kHz to MHz high-frequency range).
- Significantly outperforms traditional silicon steel or ferrite materials in effectively suppressing high-frequency voltage spikes and ripple currents generated at high switching frequencies (typical IGBT switching frequencies in the kHz range).
- High magnetic saturation strength and strong capability to withstand transient overloads.
- Key Technology 1: High-Frequency Eddy Current Suppression Coating
- Application of a special conductive coating on the nanocrystalline core or winding surface.
- Effectively dissipates ultra-high-frequency eddy current losses (frequencies up to MHz level) induced by extremely high du/dt.
- Significantly reduces core temperature rise at high frequencies, maintains stable magnetic performance, and enhances the reactor's long-term reliability under high du/dt conditions.
- Key Technology 2: Multi-Layer Sectional Winding Reducing Distributed Capacitance
- Employs a special multi-layer, sectional winding structure design.
- Divides the equivalent distributed capacitance (Cdw) of a traditional concentrated winding into multiple smaller series-connected capacitive units.
- The overall effective distributed capacitance value is significantly reduced.
- Core Value:
- Increases the reactor's self-resonant frequency well above the VFD switching frequency and harmonic frequencies, ensuring it maintains a pure inductive characteristic within the target frequency band.
- Effectively weakens the intensity of the oscillating circuit formed by the VFD's PWM high-frequency pulses and the motor cable's parasitic capacitance, fundamentally suppressing the amplitude and energy of voltage spikes (ringing).
- Reduces the flow of high-frequency oscillating current components through the reactor.
- Core Functions:
- Effectively smooths the voltage waveform, substantially reducing the output-side voltage slew rate (du/dt), bringing spikes down to safe levels.
- Filters out high-frequency harmonic currents, reducing motor harmonic losses and temperature rise.
- Suppresses voltage reflection waves (Wave Reflection).
- Reduces harmonic voltage distortion rate at the line end.
- Reduces the risk of common-mode voltage and bearing currents.
- Reduces conducted and radiated electromagnetic interference (EMI).
3. Performance Data (Applied in 550kW Rolling Mill VFD Scenario)
- Voltage Spike Suppression: Output-side du/dt is significantly reduced, with peak values dropping from >5000 V/μs to safe thresholds (e.g., <1000 V/μs or lower, specific values require field measurement confirmation), meeting motor insulation protection requirements.
- Current Limiting Capability: Effectively limits inrush currents during motor startup or sudden load changes, protecting the VFD and connections. Current limiting capability can reach 30% of the VFD's rated current.
- Reduced Voltage Distortion Rate: Effectively filters out high-frequency harmonics. Measured voltage distortion rate (THDv) at the VFD output is reduced by up to 42%, significantly improving power supply quality.
- Protection Effect: Greatly alleviates the reverse recovery surge and overvoltage stress borne by IGBT modules.
4. Economic Benefits
- Significant Extension of Critical Component Lifespan: The most direct and significant economic benefit is seen in:
- IGBT Module Lifespan Extension: Effectively reduces the electrical stress (voltage spikes, overcurrent) they endure. Measured data indicates the average service life of IGBT power modules can be prolonged by 2.3 times. As the core drive equipment of a rolling mill line, the extended lifespan of the VFD's main power components means:
- Reduced procurement quantity and inventory costs of expensive IGBT module spares.
- Significantly decreased unplanned downtime frequency and duration due to power module failures, ensuring continuous production.
- Reduced Motor Maintenance Costs:
- Effectively protects motor winding insulation, lowering motor insulation failure rates.
- Suppresses bearing currents, reducing bearing electrical erosion damage and replacement frequency.
- Extends the overall service life of motors, delaying major overhauls or replacement cycles.
- Improved System Reliability and Production Efficiency:
- Reduces the number of VFD or motor failures caused by voltage spikes, enhancing the overall operational reliability (OEE - Overall Equipment Effectiveness) of the rolling line.
- Reduces production losses, scrap risks, and order delays caused by unexpected downtime.
- Reduced Maintenance Costs: Minimizes maintenance labor hours and spare parts consumption due to equipment damage.
- Improved Power Factor (Indirectly): Improved waveform contributes to optimizing the system power factor (although primarily handled by input reactors or active compensation, output reactor waveform improvement also provides some benefit).