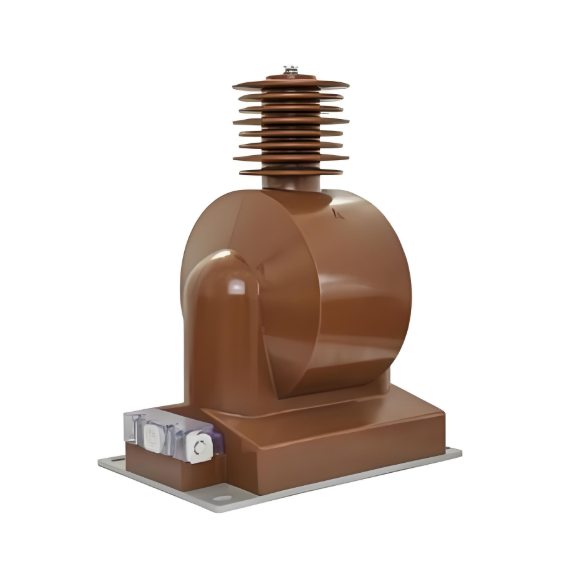
I. Industry Pain Points: Limitations of Traditional Solutions
In county-level distribution grids and infrastructure projects in developing countries, traditional Air-Insulated Switchgear Voltage Transformers (AIS VTs) face two core challenges:
- High Customization Costs: Independent housing and winding designs are required for different voltage classes (66kV/110kV/220kV), resulting in inflated R&D and manufacturing costs.
- Spare Parts Inventory Pressure: Multiple VT specifications necessitate large stocks of dedicated spare parts, tying up capital and reducing maintenance efficiency.
II. Innovative Solution: Modular Design Drives Full-Lifecycle Cost Optimization
- Standardized Voltage Module
• Core Technology: Replaceable coil bobbin frame design enables compatibility with 66kV/110kV/220kV in a single housing.
• Economic Value:
o 30% reduction in housing mold development costs;
o 25% increase in production efficiency through streamlined manufacturing.
- Detachable Secondary Terminal Box
• Rapid Replacement Design:
o Standardized interfaces enable field replacement in <1 hour (vs. ≥7 days for factory repair in traditional solutions);
o Supports individual faulty component replacement, avoiding whole-unit scrapping.
• Maintenance Cost Optimization:
o 60% reduction in spare part types, decreasing inventory costs by 45%;
o 80% shorter power outage time, enhancing supply reliability.
- Material Innovation: Aluminum Windings + Epoxy Resin Casting
• Lightweight & Cost Control:
o Aluminum windings replace copper, reducing material costs by 25%;
o Vacuum epoxy resin casting ensures insulation strength (power frequency withstand voltage ≥3kV/mm).
• Performance Validation:
o Temperature rise test ≤65K (IEC 60044 Standard);
o Accuracy Class 0.2, meeting dual requirements for metering and protection.
III. Application Scenarios and Quantified Value
Scenario
|
Core Needs
|
Solution Value
|
County Distribution Grids
|
Low budget, high reliability
|
20% lower procurement cost, 50% higher maintenance efficiency
|
Developing Country Projects
|
Rapid deployment, spare parts commonality
|
60% fewer inventory types, 40% shorter delivery cycle
|
IV. Core Advantages Summary
• Procurement Cost Optimization: 20% lower initial investment, ROI period shortened to 3 years;
• Full-Lifecycle Cost Control: Spare parts commonality + modular replacement reduces Life Cycle Cost (LCC) by 35%;
• Enhanced Sustainability: Aluminum windings cut carbon footprint by 30%, epoxy resin achieves 90% recyclability.