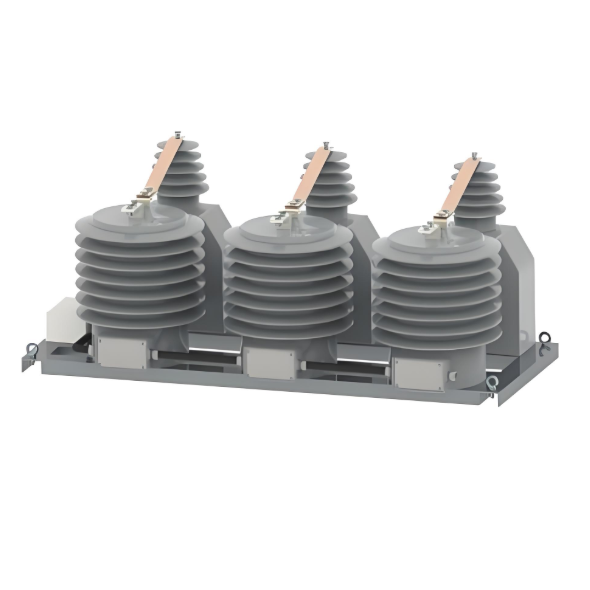
1. Core Solution Concept: Modular Platform with Shared Insulation
- Design: Develop a unified, modular platform housing both current and voltage sensing functions within a single, optimized structure.
- Insulation: Utilize a shared insulating envelope. Two options are engineered:
- SF6 Gas: Proven high-dielectric strength and excellent arc-quenching properties for higher voltage classes (e.g., 72.5 kV and above). Design incorporates gas density monitoring and proven sealing technology.
- Composite Housing (Solid Insulation): Environmentally sustainable solution using high-grade polymer materials with silicone sheds. Ideal for lower to medium voltages or where SF6 avoidance is mandated. Optimized for creepage distance and pollution performance.
- Modularity: Design internal components and interfaces to allow for:
- Scalability across different voltage classes (e.g., through insulator length adjustment).
- Adaptation to specific bushing interface requirements.
- Potential for future sensor technology upgrades.
2. Integrated Sensing Technology Implementation
- Current Measurement:
- Sensor: High-accuracy, temperature-compensated Rogowski coils. Selected for:
- Wide Dynamic Range: Excellent linearity from small fractions of nominal current up to high fault currents (e.g., >40 kA).
- No Saturation: Fundamental advantage over iron-core CTs, eliminating saturation risk during faults.
- Lightweight: Significantly reduces mechanical stress on the overall structure.
- Integration: Coils strategically placed within the insulator envelope, concentric with the primary conductor. Secure mechanical mounting resistant to vibration.
- Voltage Measurement:
- Sensor: High-stability capacitive voltage dividers (CVDs) as standard. Resistive dividers (RVDs) considered for specific DC or wide-bandwidth applications requiring fast transient response.
- Integration: CVD sensing electrodes (low-impedance) integrated directly into the insulator structure. Precision grading electrodes ensure uniform field distribution and thermal/pollution stability. Critical shielding prevents external field interference.
3. Advanced Electromagnetic Field Modeling & Isolation (Critical Engineering Challenge)
- Modeling: Mandatory, high-fidelity 3D Finite Element Method (FEM) modeling of the entire platform:
- Precisely characterizes internal electromagnetic fields under all operational conditions (sinusoidal, transient, distorted waveforms).
- Evaluates proximity effects from conductors, enclosure, and adjacent phases.
- Minimizing Crosstalk:
- Physical Separation: Optimal geometric arrangement of sensing elements (coils, CVD electrodes) based on modeling results. Maximize distance within constraints.
- Active Shielding: Implementation of grounded electrostatic shields strategically placed between sensor elements based on field simulation data.
- Guard Rings: Utilize conductive guard rings around Rogowski coil outputs to drain displacement currents.
- Precise Measurement Isolation:
- Dedicated Signal Paths: Routing signals from individual sensors using shielded, twisted-pair cabling within the enclosure immediately upon capture.
- Compensated Circuit Design: Electronic conditioning circuits designed with crosstalk cancellation techniques informed by FEM models.
- Validation: Rigorous factory testing (including harmonic injection tests) to characterize and verify isolation margins and crosstalk levels (< 0.1% specified).
4. Integrated Digital Processing & Standardized Interfaces
- Onboard Signal Processing:
- Dedicated, low-power ASICs or high-reliability microcontrollers directly integrated onto the sensor platform or adjacent sealed module.
- Functions include: Rogowski coil integrator, scaling, ADC conversion, harmonic computation (if applicable), linearization, temperature compensation, and timestamping.
- Standardized Digital Output:
- Embedded Interfaces: Incorporate IEC 61869 compliant digital output circuitry directly within the CIT unit.
- Protocols: Standardized support for:
- IEC 61850-9-2: Sampled Values (SV) stream over Ethernet (typically multicast).
- IEC 61850-9-3LE: Lightning Edition SV profile for guaranteed low-latency determinism.
- Additional Options: Provision for legacy outputs (analog, IEC 60044-8 FT3) where required via optional modules.
- Data Quality: Integrated Merging Unit (MU) functionality meeting relevant IEC 61869 accuracy (TPE/TPM class) and timing (PLL synchronization) standards.
5. Engineering Design & Integration Considerations
- Thermal Management: Models include thermal performance analysis. Power dissipation from electronics actively managed using low-power components, potential localized heatsinks, and optimized convection paths within the insulator.
- EMC/EMI Robustness: Conformal coating, shielded enclosures, ferrites, and optimized grounding strategies applied to internal electronics. Surge protection compliant with relevant standards (IEC 61000-4-5).
- Mechanical Integrity: Structural analysis performed for seismic loads, wind loading, ice loading, and dynamic forces during faults. Optimized use of materials (composite/porcelain/SF6) contributes to lower seismic mass.
- Factory Calibration & Testing: Comprehensive calibration against reference standards (optical/VTBI methods). Includes verification of EM isolation effectiveness, timing accuracy, protocol compliance, and full-power dielectric testing.
- Lifecycle & Serviceability: Designed for minimal maintenance (especially SF6 or solid insulation). Modular electronics potentially accessible/testable without major disassembly. End-of-life disposal pathways considered (SF6 recovery/recycling).
Benefits Realized through this Design & Integration Approach:
- Footprint Reduction: Up to 40-50% space savings vs. separate CTs/VTs – crucial for retrofits and compact GIS/AIS designs.
- Enhanced Accuracy & Safety: Eliminates traditional CT saturation risks, improves transient response (Rogowski/CVD), reduces external connections/risks.
- Simplified Installation: Single unit mounting and commissioning significantly reduce field labor and cabling complexity.
- Lower Lifecycle Costs: Reduced installation, cabling, civil work, maintenance overhead.
- Digital Substation Readiness: Direct IEC 61850-9-2/3LE output enables seamless integration into modern protection, control, and monitoring systems (SAS).
- Future-Proof Platform: Modular design accommodates evolving sensor technologies and communication standards.
- Reduced Environmental Impact (Solid Insulation Option): Eliminates SF6 usage and associated risks.