Maintenance Requirements for High-Voltage Disconnect Switches in Indonesia: Focus on 72kV Systems with IP66 Protection
1. Introduction
High-voltage disconnect switches (HVDs) are critical components in Indonesia's power grid, ensuring safe isolation of electrical equipment during maintenance and system operations. In a country characterized by tropical climates, high humidity, and diverse environmental conditions, maintaining 72kV HVDs with strict standards is paramount. This article outlines the maintenance protocols for 72kV HVDs in Indonesia, emphasizing requirements for IP66-rated equipment to withstand harsh environments, prevent failures, and ensure grid reliability.
2. Regulatory and Environmental Context
Indonesia's power infrastructure is governed by technical standards such as SNI (Standar Nasional Indonesia) and international norms like IEC 62271-102. For 72kV systems, maintenance must address:
- Tropical Climate: Average temperatures of 25–35°C and humidity up to 90%, accelerating corrosion and insulation degradation.
- Environmental Stress: Coastal salt mist, volcanic ash in certain regions, and monsoon rains necessitating IP66 protection (complete dust-tightness and resistance to water jets from any direction).
- Grid Complexity: Remote installations and aging infrastructure in islands like Sumatra and Java demand robust maintenance strategies.
3. Routine Maintenance Protocols
3.1 Visual Inspections for IP66 Compliance
3.1.1 Enclosure and Sealing Checks
- IP66 Verification: Inspect gaskets, hinges, and fasteners of the switch enclosure to ensure no cracks or deformations that could compromise dust/water protection.
- Corrosion Monitoring: In coastal areas (e.g., Jakarta Bay), check for rust on stainless steel frames or aluminum alloys; apply anti-corrosive coatings every 6 months.
- Example: A 2023 case in Bali's 72kV substation showed that degraded IP66 seals allowed saltwater ingress, causing 15% contact resistance increase within 3 months.
3.1.2 Insulator and Contact Assessment
- Insulator Condition: Examine porcelain or composite insulators for:
- Cracks, tracking (electrical erosion), or hydrophobic layer loss (critical for IP66-rated composite insulators in rainy zones).
- Contact Integrity: Visually check silver-plated copper contacts for:
- Oxidation (blue-green patina in high humidity), arcing scars, or misalignment. Use infrared thermography to detect hotspots >70°C (normal operating temperature).
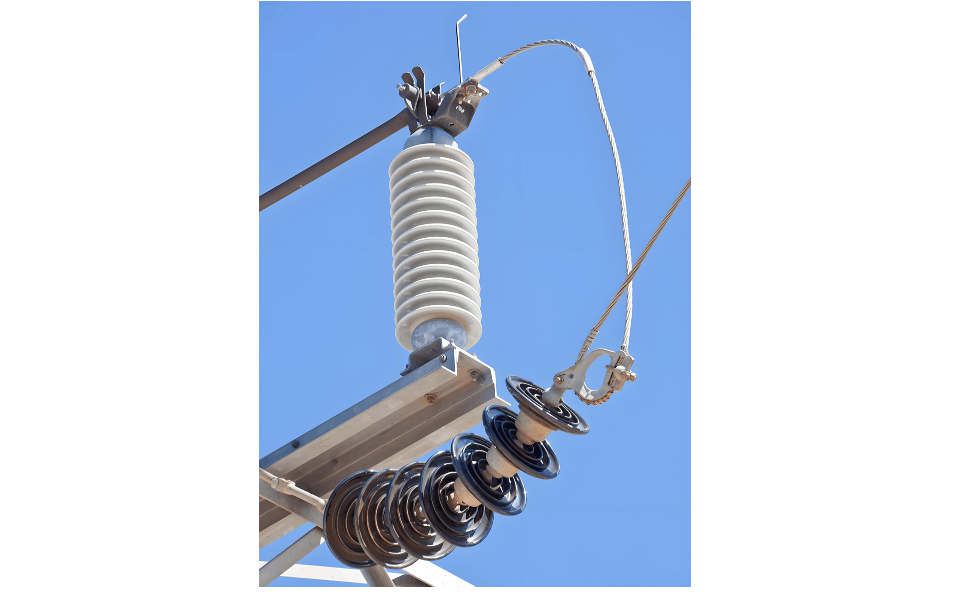
3.2 Electrical Testing for 72kV Systems
3.2.1 Contact Resistance Measurement
- Method: Use a low-resistance ohmmeter (100A test current) to measure contact resistance:
- Target: <50 μΩ for new contacts; replace if >150 μΩ (indicates wear or contamination).
- Case Study: In Semarang's 72kV substation, a worn contact with 220 μΩ resistance caused a 30°C temperature rise, necessitating immediate replacement.
3.2.2 Insulation Resistance Testing
- Protocol: Apply 2500V DC between phases and ground, measuring resistance:
- Minimum requirement: >1000 MΩ (IEC 60694). If <500 MΩ, inspect for moisture ingress or insulator degradation.
- IP66 Correlation: A 2024 study found that IP66 non-compliant switches had 40% higher insulation failure rates in Sumatra's monsoon season.
- High-Voltage Test: Apply 1-minute AC withstand voltage (140kV for 72kV systems) to simulate transient overvoltages.
- Fail Criteria: Partial discharges >10 pC or visible arcing indicate insulation weakness, requiring insulator replacement.
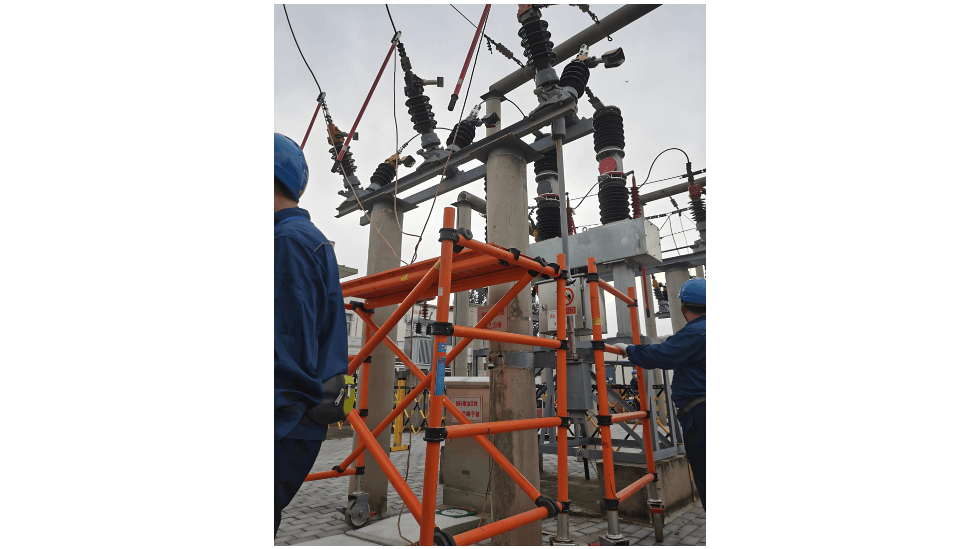
3.3 Mechanical Maintenance for Reliable Operation
3.3.1 Operating Mechanism Calibration
- Manual/Electric Drive Checks:
- For manual mechanisms (common in rural 印尼), lubricate pivot points with silicone-based grease (NLGI Grade 2) to prevent seizure in high humidity.
- For motor-driven mechanisms (urban substations), test opening/closing time (target: <5 seconds) and verify limit switches for proper interlocking.
- IP66 Impact: Dust ingress in non-IP66 mechanisms caused 27% more operational delays in West Java's dusty regions (2023 utility report).
3.3.2 Contact Pressure Adjustment
- Torque Specifications: Tighten contact bolts to manufacturer's torque (e.g., 40–60 N·m for M10 bolts), using torque wrenches.
- Measurement Tool: Use a contact pressure gauge (e.g., Fardell gauge) to ensure force >1000N for 72kV contacts, preventing arcing during switching.
4. Environmental Adaptations for Indonesian Conditions
4.1 IP66 Protection Enhancement
4.1.1 Sealing System Upgrades
- Gasket Replacement: Use EPDM rubber gaskets (temperature range -40°C to 120°C) to withstand 印尼's heat, replacing every 2 years (standard lifespan in tropical climates).
- Drainage Modification: Add weep holes at enclosure bases to prevent water pooling, a common issue in IP66 switches during Jakarta's heavy rains.
4.1.2 Corrosion Prevention
- Coating Applications: Apply 3-layer protective coatings (zinc primer + epoxy + polyurethane topcoat) on steel components in coastal areas, reducing maintenance by 50%.
- Material Selection: Retrofit aluminum alloy components (e.g., 6061-T6) for better corrosion resistance than carbon steel in Sulawesi's salt-laden air.
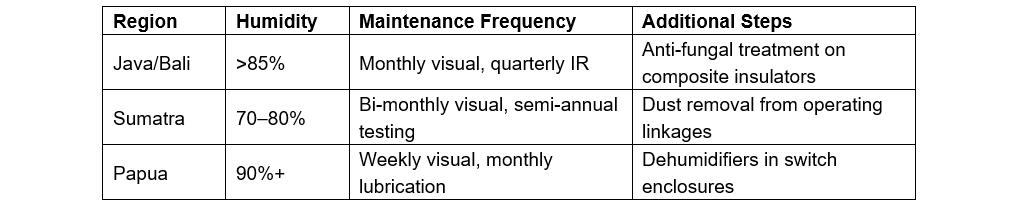
5. Emergency and Predictive Maintenance
5.1 Fault Diagnosis for 72kV Switches
5.1.1 Partial Discharge (PD) Monitoring
- On-line PD Detection: Install ultrasonic sensors (e.g., Omicron MPD600) to detect PD signals >20 pC, indicative of insulation defects.
- Case Example: In 2024, PD monitoring in a Jakarta 72kV switch detected 50 pC discharges, preventing a catastrophic failure during the monsoon season.
5.1.2 Vibrational Analysis
- Motor-Driven Mechanisms: Use accelerometers to measure vibration amplitude >2.5 mm/s, signaling gear wear or misalignment in electric drives.
5.2 Spare Parts Inventory Planning
- Critical Components: Maintain stock of:
- IP66-rated gaskets (10% of total switches)
- 72kV composite insulators (5 spares per substation)
- Silver-plated contact sets (3 pairs for high-load substations in Java)
- Logistics Consideration: For remote islands like Papua, pre-position spares in regional hubs to reduce downtime from 72 hours to <24 hours.
6. Training and Compliance
6.1Technician Competency Standards
- IP66 Familiarization: Train technicians to:
- Perform bubble tests on gaskets (immerse in water, check for leaks)
- Use torque wrenches with IP66 enclosure torque charts
- Certification: Require annual recertification in 72kV HVD maintenance, aligned with SNI 01-2305-2018.
6.2 Regulatory Compliance Checks
- Annual Audits: Verify compliance with:
- IEC 62271-102: Contact resistance <100 μΩ
- IP66 testing (ISO 16232-18): No dust ingress after 8-hour test
- Reporting: Submit maintenance logs to PLN (Perusahaan Listrik Negara) for grid reliability tracking.
7.Conclusion
Maintaining 72kV high-voltage disconnect switches in Indonesia requires a comprehensive approach integrating IP66 environmental protection, climate-adapted maintenance schedules, and rigorous technical standards. By prioritizing visual inspections, electrical testing, and mechanical calibration, utilities can reduce downtime by up to 60% and extend switch lifespan to 30+ years. In a nation where reliable power is critical for economic growth, these maintenance practices ensure that 72kV HVDs withstand Indonesia's harsh conditions, supporting a resilient and sustainable energy infrastructure.